THE CHALLENGE
Additive manufacturing (AM) has emerged as a powerful tool within engineering. Many AM and coating processes rely on thermal input to soften or melt the materials involved in processing. However, this melting or softening typically results in a higher thermal gradient between deposited material and the workpiece, commonly resulting in defects such as residual stress and warpage.
OUR SOLUTION
The Yu lab has developed AM techniques, leveraging an enclosed area which is selectively filled with solids, liquids, and/or gasses which themselves are held at desired temperatures. Based on the temperature of the added substances and their heat transfer rates, the workpiece can be held at specific target temperatures, or have specific thermal gradients applied to them. Additionally, by separating materials through buoyancy, temperature, and applied films/barriers, multiple temperatures and thermal gradients can be assigned to a workpiece as it is processed. This enables discrete control over the thermal history of the processed materials at an unprecedented level, drastically improving the quality of the deposited material.
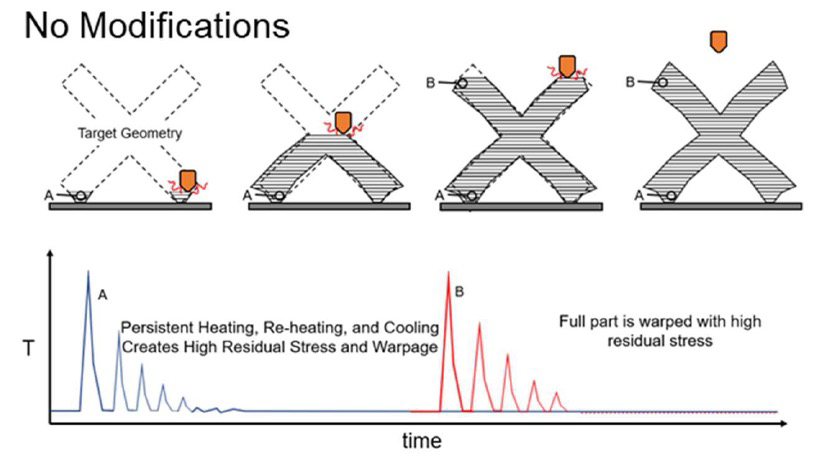
Thermal mismatch during cooling or solidification can result in severe residual stress or even warpage in AM parts or in coating/cladding processes, due to a failure to create uniform or controlled thermal history for every section of a workpiece.
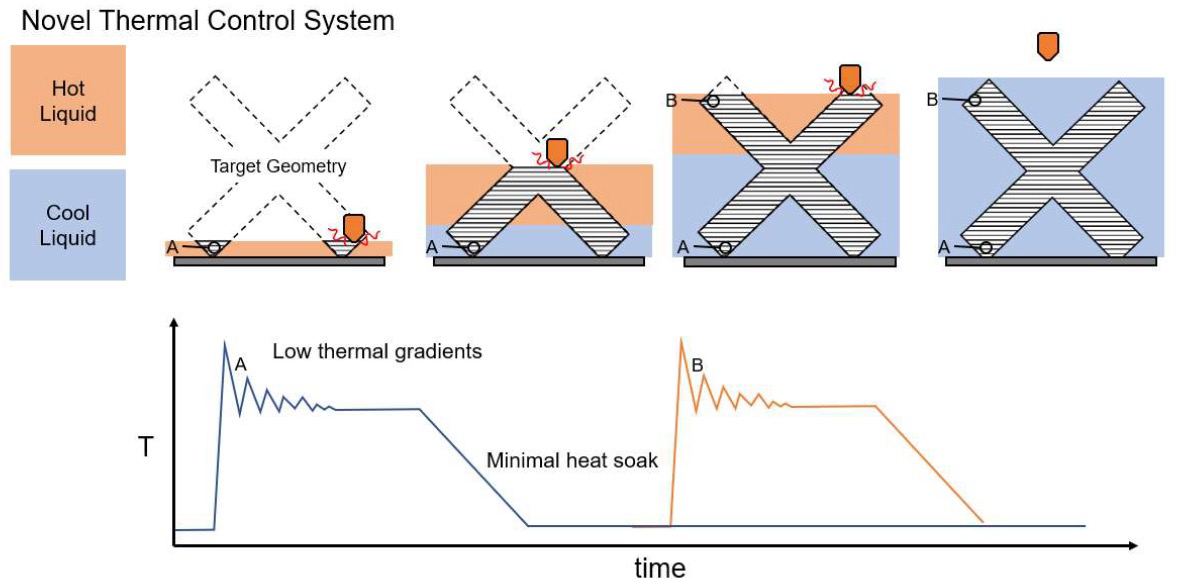
Regions near the direct processing zone of the workpiece can be held at elevated temperatures minimizing residual stresses. A smooth gradient to the rest of the workpiece can be achieved through temperature control of the secondary/tertiary medium. In this case, hot liquid (orange) is interfaced with a cool liquid (blue) to eliminate warpage to the workpiece.