THE CHALLENGE
Functional emulsions are an emerging material architecture that can be cured into an elastomer composite with embedded liquid phase fillers. Techniques to control local composite microstructures and material composition in emulsions, which ultimately govern material properties and performance of the cured elastomer composite, are lacking.
OUR SOLUTION
The Bartlett lab at Virginia Tech has developed additive manufacturing techniques to program liquid inclusion microstructure in emulsions to achieve unprecedented combinations of thermal, electrical and mechanical functionalities in elastomer composites. By controlling various parameters of the print such as nozzle speed, elastomers with markedly different physical characteristics such as Z-dimensionality and electrical conductivity are made. These techniques can be broadly applied to various liquid metal inclusions. Furthermore, this technique is scalable and can be readily integrated into present additive manufacturing setups in industry.
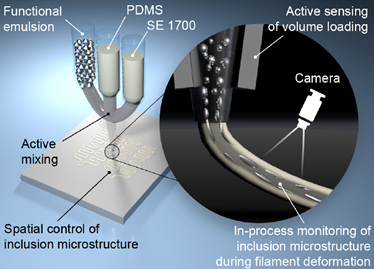
Figure : Manufacturing strategy for controlling the special inclusion morphology and composition of functional emulsions.