THE CHALLENGE
The mining industry faces a major business and sustainability challenge: the energy-intensive process of grinding ore to extract valuable minerals is consuming up to 4% of global electricity and nearly half of a mine’s on-site energy—driving up operational costs and carbon emissions. Traditional solutions like larger ball mills, high-pressure grinding rolls, and grinding aids offer only limited efficiency gains, especially as ores become harder and more complex. Meanwhile, methods like flotation struggle to recover valuable minerals from coarser particles, forcing even finer grinding, which increases energy demands and processing costs. Emerging technologies such as carbon mineralization and bioleaching show promise for reducing energy use and capturing CO₂, but they remain too slow, expensive, or difficult to scale. For mining companies, this means a growing gap between production goals and environmental or economic realities—creating an urgent need for scalable, cost-effective innovations that improve mineral liberation while cutting both energy consumption and emissions.
OUR SOLUTION
We offer a game-changing, energy-efficient alternative to traditional mineral processing by using supercritical CO₂ treatment to chemically weaken ore before grinding. This approach can reduce energy use by up to 50%, significantly lowering both operational costs and emissions. Key to this innovation is the use of CO₂ not just as a processing aid but also as a carbon sequestration tool, forming stable carbonates while enhancing mineral liberation. This system supports global decarbonization goals and offers mining companies a scalable, cost-effective pathway to reduced environmental impact and improved processing efficiency.
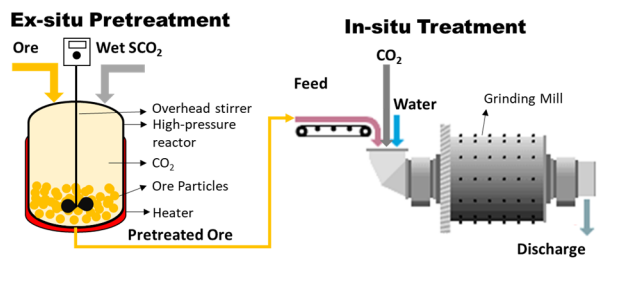
Figure: Comminution energy reduction by carbonation.
Advantages:
- ~50% reduction in comminution energy
- Carbon-negative processing with integrated CO₂ sequestration
- Coarse-particle recovery via HydroFloat (1–0.15 mm)
- Energy cost cut from ~$1.6/ton to ~$0.28/ton
Potential Application:
- Carbon-negative copper and rare earth beneficiation
- Tailings reprocessing with CO₂ sequestration
- Equipment retrofitting for energy-efficient grinding
- Bioleaching of sulfide ores with CO₂ fixation