THE CHALLENGE
The challenge lies in developing a cost-effective, scalable process that can both capture CO₂ and extract critical energy metals from ultramafic and mafic rocks, especially mine tailings. Currently, these two goals are tackled separately using energy-intensive and chemically harsh methods that are expensive, waste-generating, and often counterproductive—such as releasing captured CO₂ during metal purification. Efforts to combine them into a single system have struggled due to technical issues like metal co-precipitation with common minerals, complex downstream separation, and equipment corrosion under harsh conditions. These inefficiencies translate to high operational costs, low metal recovery yields, and limited return on investment, making it difficult to attract financing or scale operations. Bridging this gap requires a breakthrough approach that integrates carbon capture and metal recovery in a way that is both economically viable and environmentally sustainable.
OUR SOLUTION
We offer a groundbreaking, single-step process that simultaneously captures CO₂ and recovers valuable metals like nickel and cobalt from ultramafic and mafic rocks, including mine tailings—turning a major waste stream into a revenue-generating resource. By using supercritical CO₂ (scCO₂) in water to break down minerals and form stable carbonates, the process permanently stores carbon while specialized extractants keep critical metals in solution for efficient recovery. Unlike conventional methods that rely on aggressive acids, high energy inputs, and complex multi-step workflows, our approach reduces chemical use, energy demand, and waste generation—cutting both costs and environmental impact. This integrated system not only boosts profitability by unlocking high-purity metal products but also offers a scalable, carbon-negative technology for industries looking to meet both decarbonization goals and growing demand for energy-transition minerals.
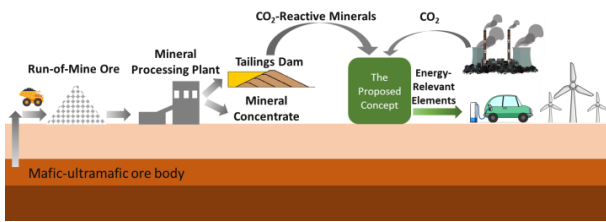
Figure: Schematic summary of the concept.
Advantages:
- Integrated CO₂ sequestration and metal extraction in a single reactor
- Elimination of aggressive acids and reduced chemical usage
- High-purity (>99%) recovery of Ni/Co with >80% yield
- Up to 60% lower energy consumption than conventional methods
Potential Application:
- EV battery-grade nickel and cobalt production
- Carbon capture and permanent mineral sequestration
- Rare earth element recovery from mine tailings
- Sustainable mine waste valorization